3d Car Wallpaper Definition
Source (google.com.pk)As their name implies, four-stroke internal combustion engines have four basic steps that repeat with every two revolutions of the engine:
(1) Intake/suction stroke (2) Compression stroke (3) Power/expansion stroke and (4) Exhaust stroke
1. Intake stroke: The first stroke of the internal combustion engine is also known as the suction stroke because the piston moves to the maximum volume position (downward direction in the cylinder). The inlet valve opens as a result of the cam lobe pressing down on the valve stem, and the vaporized fuel mixture enters the combustion chamber. The inlet valve closes at the end of this stroke.
2. Compression stroke: In this stroke, both valves are closed and the piston starts its movement to the minimum volume position (upward direction in the cylinder) and compresses the fuel mixture. During the compression process, pressure, temperature and the density of the fuel mixture increases.
3. A Power stroke: When the piston reaches a point just before top dead center, the spark plug ignites the fuel mixture. The point at which the fuel ignites varies by engine; typically it is about 10 degrees before top dead center. This expansion of gases caused by ignition of the fuel produces the power that is transmitted to the crank shaft mechanism.
4. Exhaust stroke: In the end of the power stroke, the exhaust valve opens. During this stroke, the piston starts its movement in the maximum volume position. The open exhaust valve allows the exhaust gases to escape the cylinder. At the end of this stroke, the exhaust valve closes, the inlet valve opens, and the sequence repeats in the next cycle. Four-stroke engines require two revolutions.
Many engines overlap these steps in time; turbine engines do all steps simultaneously at different parts of the engines.
All internal combustion engines depend on combustion of a chemical fuel, typically with oxygen from the air (though it is possible to inject nitrous oxide to do more of the same thing and gain a power boost). The combustion process typically results in the production of a great quantity of heat, as well as the production of steam and carbon dioxide and other chemicals at very high temperature; the temperature reached is determined by the chemical make up of the fuel and oxidisers (see stoichiometry), as well as by the compression and other factors.
The most common modern fuels are made up of hydrocarbons and are derived mostly from fossil fuels (petroleum). Fossil fuels include diesel fuel, gasoline and petroleum gas, and the rarer use of propane. Except for the fuel delivery components, most internal combustion engines that are designed for gasoline use can run on natural gas or liquefied petroleum gases without major modifications. Large diesels can run with air mixed with gases and a pilot diesel fuel ignition injection. Liquid and gaseous biofuels, such as ethanol and biodiesel (a form of diesel fuel that is produced from crops that yield triglycerides such as soybean oil), can also be used. Engines with appropriate modifications can also run on hydrogen gas, wood gas, or charcoal gas, as well as from so-called producer gas made from other convenient biomass. Recently, experiments have been made with using powdered solid fuels, such as the magnesium injection cycle.
Internal combustion engines require ignition of the mixture, either by spark ignition (SI) or compression ignition (CI). Before the invention of reliable electrical methods, hot tube and flame methods were used. Experimental engines with laser ignition have been built.Gasoline engine ignition systems generally rely on a combination of a lead–acid battery and an induction coil to provide a high-voltage electric spark to ignite the air-fuel mix in the engine's cylinders. This battery is recharged during operation using an electricity-generating device such as an alternator or generator driven by the engine. Gasoline engines take in a mixture of air and gasoline and compress it to not more than 12.8 bar (1.28 MPa), then use a spark plug to ignite the mixture when it is compressed by the piston head in each cylinder.
While gasoline internal combustion engines are much easier to start in cold weather than diesel engines, they can still have cold weather starting problems under extreme conditions. For years the solution was to park the car in heated areas. In some parts of the world the oil was actually drained and heated over night and returned to the engine for cold starts. In the early 1950s the gasoline Gasifier unit was developed, where part on cold weather starts raw gasoline was diverted to the unit where part of the gas was burned causing the other part to become a hot vapor sent directly to the intake valve manifold. This unit was quite popular till electric engine block heaters became standard on gasoline engines sold in cold climates.
Diesel engines and HCCI (Homogeneous charge compression ignition) engines, rely solely on heat and pressure created by the engine in its compression process for ignition. The compression level that occurs is usually twice or more than a gasoline engine. Diesel engines take in air only, and shortly before peak compression, spray a small quantity of diesel fuel into the cylinder via a fuel injector that allows the fuel to instantly ignite. HCCI type engines take in both air and fuel, but continue to rely on an unaided auto-combustion process, due to higher pressures and heat. This is also why diesel and HCCI engines are more susceptible to cold-starting issues, although they run just as well in cold weather once started. Light duty diesel engines with indirect injection in automobiles and light trucks employ glowplugs that pre-heat the combustion chamber just before starting to reduce no-start conditions in cold weather. Most diesels also have a battery and charging system; nevertheless, this system is secondary and is added by manufacturers as a luxury for the ease of starting, turning fuel on and off (which can also be done via a switch or mechanical apparatus), and for running auxiliary electrical components and accessories. Most new engines rely on electrical and electronic engine control units (ECU) that also adjust the combustion process to increase Engines based on the two-stroke cycle use two strokes (one up, one down) for every power stroke. Since there are no dedicated intake or exhaust strokes, alternative methods must be used to scavenge the cylinders. The most common method in spark-ignition two-strokes is to use the downward motion of the piston to pressurize fresh charge in the crankcase, which is then blown through the cylinder through ports in the cylinder walls.
Spark-ignition two-strokes are small and light for their power output and mechanically very simple; however, they are also generally less efficient and more polluting than their four-stroke counterparts. In terms of power per cm³, a two-stroke engine produces comparable power to an equivalent four-stroke engine. The advantage of having one power stroke for every 360° of crankshaft rotation (compared to 720° in a 4-stroke motor) is balanced by the less complete intake and exhaust and the shorter effective compression and power strokes. It may be possible for a two-stroke to produce more power than an equivalent four-stroke, over a narrow range of engine speeds, at the expense of less power at other speeds.
Small displacement, crankcase-scavenged two-stroke engines have been less fuel-efficient than other types of engines when the fuel is mixed with the air prior to scavenging allowing some of it to escape out of the exhaust port. Modern designs (Sarich and Paggio) use air-assisted fuel injection, which avoids this loss and provides more efficiency than comparably sized four-stroke engines. Fuel injection is essential for a modern two-stroke engine for it to meet stringent emission standards. The problem of total loss oil consumption, however, remains a cause of high hydrocarbon emissions. The low-pressure direct gasoline injection developed by R Sarich was tested by Ford in an automobile size 2-stroke engine, and in 2012, Orbital won a contract by the Australia government for a two-stroke, direct injection engine for airborne drones.
3d Car Wallpaper Free Wallpaper Pics Pictures Hd for Desktop Iphone Mobile HD 1080p

3d Car Wallpaper Free Wallpaper Pics Pictures Hd for Desktop Iphone Mobile HD 1080p

3d Car Wallpaper Free Wallpaper Pics Pictures Hd for Desktop Iphone Mobile HD 1080p

3d Car Wallpaper Free Wallpaper Pics Pictures Hd for Desktop Iphone Mobile HD 1080p

3d Car Wallpaper Free Wallpaper Pics Pictures Hd for Desktop Iphone Mobile HD 1080p
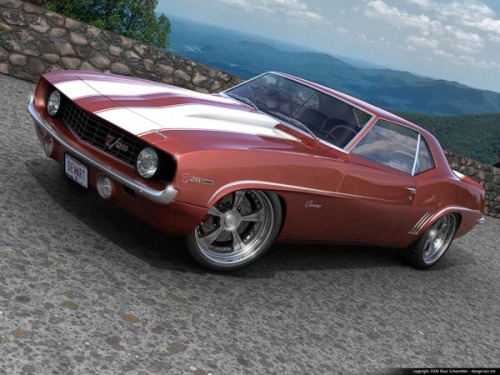
3d Car Wallpaper Free Wallpaper Pics Pictures Hd for Desktop Iphone Mobile HD 1080p

3d Car Wallpaper Free Wallpaper Pics Pictures Hd for Desktop Iphone Mobile HD 1080p

3d Car Wallpaper Free Wallpaper Pics Pictures Hd for Desktop Iphone Mobile HD 1080p

3d Car Wallpaper Free Wallpaper Pics Pictures Hd for Desktop Iphone Mobile HD 1080p

3d Car Wallpaper Free Wallpaper Pics Pictures Hd for Desktop Iphone Mobile HD 1080p
